إن التوقف غير المخطط له، أو الوقت الذي يتم قضاؤه في إجراء الصيانة على الأجهزة التي تتعطل بشكل غير متوقع، يمكن أن يكلف الشركة الكثير من حيث الوقت والعمليات المفقودة والموارد البشرية. يعد نظام مراقبة الاهتزاز أداة للبحث عن المخالفات وغيرها من الحالات الشاذة في صحة الماكينة عن طريق قياس مستويات الاهتزاز. فهو يساعد على حماية المرافق والعمليات والأشخاص. يمكن للنظام التعرف على أي شيء بدءًا من عدم التوازن وعدم المحاذاة إلى الأجزاء السائبة والمساعدة في منع توقف الماكينة عن العمل. تعد أنظمة مراقبة الاهتزاز، وحتى أنظمة مراقبة الاهتزاز أحادية القناة، إحدى أكثر الطرق فعالية للتنبؤ بمشاكل الماكينة المحتملة وتوفير إنذار مبكر لأعطال الماكينة. بالنسبة للعديد من الصناعات، يعد الأمان والحفاظ على سير العمليات أمرًا بالغ الأهمية.
كيف يعمل نظام مراقبة الاهتزازات؟
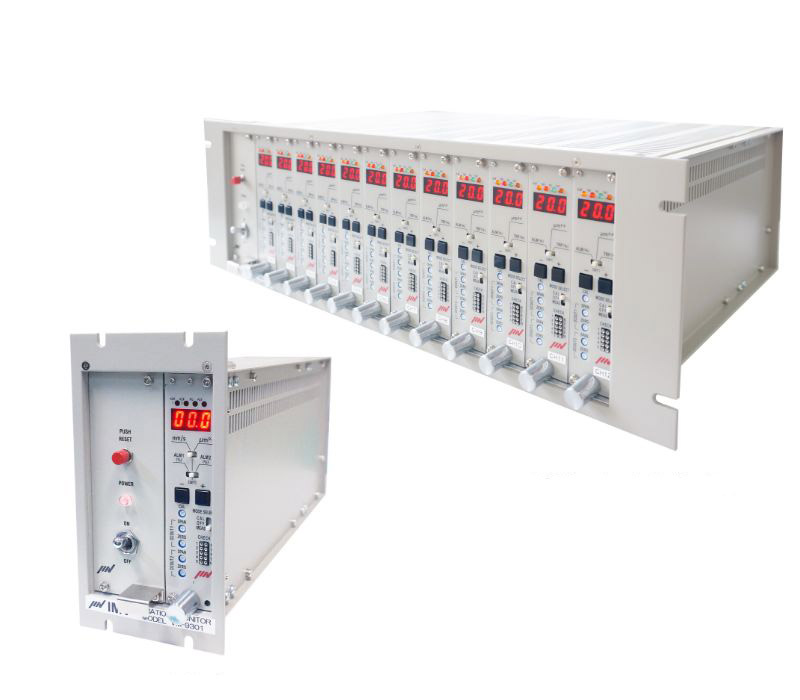
تعمل أنظمة مراقبة الاهتزاز باستخدام طريقة تسمى تحليل اتجاه الاهتزاز. تحليل اتجاه الاهتزاز هو عملية مراقبة خصائص الاهتزاز غير الطبيعية للآلة. عندما ترتفع سعة الاهتزاز أو تنخفض بشكل ملحوظ في ظل ظروف الحالة المستقرة، فهذا يشير عادةً إلى أن شيئًا ما قد تغير داخل الجهاز. السعة الإجمالية هي المؤشر الرئيسي لفشل الماكينة وهي مثالية لإخراج 4-20 مللي أمبير لأنظمة التحكم (PLC، SCADA، RTU، إلخ). تتضمن السعة الإجمالية مختلف الترددات والسعات الفردية التي تنتجها مكونات الآلة، وحركتها الدورانية أو الترددية، و/أو مشكلات العملية. تسجل بعض أنظمة المراقبة أشكال موجية الاهتزازات وتحدد مشاكل الماكينة المحتملة من خلال الكشف عن الحالات الشاذة في الاهتزازات المسجلة.
خاصية الاهتزاز
الخصائص الرئيسية للاهتزاز هي السعة والتردد والمرحلة والشكل، وعند استخدام أجهزة استشعار القرب، والموضع. تشير السعة إلى شدة الاهتزازات المرتبطة بها. التردد يساعد على تحديد مصدر الاهتزاز. قد تشير أيضًا التغييرات في تردد الاهتزاز بشكل مستقل عن التغيرات في سرعة الماكينة إلى وجود مشكلة. يمكن أن يؤدي الاهتمام بالترددات إلى تحديد مشكلات معينة بسرعة. تساعد المرحلة في تحديد متى وأين تحدث الاهتزازات. عند دراسة الشكل الموجي لاهتزاز معين، فإن السعة والتردد المتغيرين يمكن أن يكشفا الكثير عن الآلة المعنية. يمكن للسعة التي يتم قياسها بواسطة نظام مراقبة الاهتزاز أن تظهر الفرق في الحركة من وقت بدء تشغيل الماكينة إلى اللحظة المحددة التي قد يكون فيها جزء ما به مشكلة أو مشكلة. يمكن ملاحظة استخدام أجهزة استشعار القرب، أو موضع الدوار في خلوص المحمل، أو الحركة المحورية للدوار، وهو أمر مهم عند تقييم حالة الماكينة. في معظم الحالات، تستخدم أنظمة مراقبة الاهتزاز السعة الإجمالية للمقارنة مع حدود الاهتزاز أو قيم الإنذار.
كيف يتم قياس الاهتزازات؟
على الرغم من أن الاهتزاز يتم تسجيله باستخدام التردد والسعة، إلا أنه يتم قياسه من حيث التسارع والسرعة والإزاحة. يمكن مراقبة هذه الخصائص باستخدام أجهزة الاستشعار ومعدات تحليل الاهتزازات. وقد يختلف الجهاز في العناصر التي يقيسها، وكيفية قياسه.
على سبيل المثال، غالبًا ما تتم مراقبة الآلات ذات المحامل الدوارة (REBs) باستخدام أجهزة استشعار الاهتزاز الزلزالي (أجهزة استشعار السرعة أو مقاييس التسارع). عادةً ما تستخدم أجهزة REB التي تعمل بترددات أقل من 60 هرتز أجهزة استشعار السرعة. تتم عادةً مراقبة الآلات ذات محامل الأفلام الزيتية (محامل المجلات أو محامل الأكمام) باستخدام مستشعرات مسبار القرب.
تستخدم مقاييس التسارع عادةً بلورات كهرضغطية (مستشعرات PZT)، والتي تولد شحنة كهربائية عند اكتشاف أي تغيير في التسارع أو الضغط أو القوة. يمكن أيضًا تصميم مقاييس التسارع لاستخدام تقنية MEMS (النظام الكهروميكانيكي الصغير) لقياس التسارع. يمكن لأجهزة استشعار السرعة أخذ مخرجات مقياس تسارع مضخم (كهرضغطية أو MEMS)، ودمج الإشارة، ثم إخراج إشارة السرعة. في تطبيقات درجات الحرارة المرتفعة، غالبًا ما تستخدم مستشعرات سرعة الملف المتحرك لقياس الاهتزاز باستخدام السرعة. تُستخدم مجسات القرب لقياس الحركة النسبية بين سطح الدوار والمحمل، عادةً باستخدام محامل ذات طبقة زيتية. يقيس مسبار القرب الاهتزاز والموضع المحوري وسرعة الدوار. يمكن رقمنة إشارة الاهتزاز الصادرة عن المستشعر وتسجيلها لتحليل الاتجاه.
طرق مراقبة الاهتزاز الشائعة

1. المشي/جمع الاهتزازات الدورية
عادةً ما يستخدم هذا النوع من المراقبة مقياس التسارع لتسجيل مستوى الاهتزاز لكل محمل شعاعي ومحوري للآلة على أساس منتظم، عادةً شهريًا أو ربع سنوي. ولا يستخدم بيانات عابرة (بيانات البدء والإغلاق) وهو مجهز بشكل أفضل بمفاتيح اهتزاز (كهربائية أو ميكانيكية)، مما يساعد على منع تعطل الجهاز بين كل عملية تشغيل دورية للبيانات.
2. قم بالتجول حول جمع بيانات الاهتزاز (مع الشكل الموجي أو البيانات العابرة)
يتم تنفيذ ذلك عادةً بعد اكتشاف مشكلة أثناء عملية جمع بيانات الدورية، أو عندما يقوم مفتاح الاهتزاز بإيقاف تشغيل الجهاز.
3. مراقبة الاهتزاز المستمر (لا يوجد شكل موجي أو بيانات عابرة)
غالبًا ما تكون أنظمة المراقبة هذه مجهزة بوظائف الإنذار وإيقاف التشغيل للمساعدة في منع أعطال الماكينة. يستخدم هذا النوع من المراقبة أجهزة إرسال توفر إشارات من 4 إلى 20 مللي أمبير (مللي أمبير) متصلة مباشرة بنظام التحكم لمراقبة بيانات الاهتزاز.
4. مراقبة الاهتزاز المستمر (مع ارتباط بيانات العملية، بدون شكل موجي أو بيانات عابرة)
يجمع مفهوم المراقبة هذا بين وظائف الإنذار وإيقاف التشغيل للمساعدة في منع أعطال الماكينة وتحديد الاتجاهات غير الطبيعية. يتم إرسال البيانات باستخدام أجهزة إرسال من 4 إلى 20 مللي أمبير متصلة مباشرة بنظام التحكم، والتي تم ربطها بـ "شبكة معلومات المصنع" لربطها بمعلومات العملية (الحمل، التدفق، المستوى، الضغط، درجة الحرارة، إلخ). توفر بيانات الاهتزاز، إلى جانب بيانات العملية، درجة أعلى من الفهم للتشغيل الفعلي للآلة.
5. مراقبة الاهتزاز المستمر (المتعلق ببيانات العملية)
تساعد أجهزة المراقبة أحادية أو متعددة القنوات المزودة بوظائف التنبيه والإيقاف على منع أعطال الماكينة وتحديد اتجاهات الاهتزاز بسهولة. عندما يكون لديك مجموعة المستشعرات المناسبة، يتيح لك هذا النوع من المراقبة أيضًا إجراء عمليات التشخيص على الجهاز. عادةً ما يتم تضمين بيانات الاهتزاز والسرعة وموضع الدفع والتأثير في مجموعة البيانات.
6. مراقبة الاهتزاز المستمر (مع ارتباط بيانات العملية والشكل الموجي والبيانات العابرة)
يتمتع هذا النوع من المراقبة بنفس الوظائف المذكورة أعلاه، مما يسمح لك بتحديد الاتجاهات غير الطبيعية ومنع فشل الماكينة في ظل ظروف المعالجة العادية. يمكنك أيضًا تشغيل تشخيصات الماكينة عند الطلب واستخدام المستشعرات المدمجة مع بيانات عملية المصنع. وهذا هو أعلى شكل من أشكال مراقبة الاهتزازات الميكانيكية.
التطبيقات الشائعة لأنظمة مراقبة الاهتزاز
يمكن استخدام أنظمة مراقبة الاهتزاز لمجموعة متنوعة من التطبيقات المختلفة. فيما يلي بعض الاستخدامات الصناعية الأكثر شيوعًا:
من المهم ملاحظة أن عدد أجهزة استشعار الاهتزاز المستخدمة في الآلات الدوارة أو الترددية يعتمد على مدى أهمية المعدات. يجب أن يتم تزويد المعدات الحيوية، التي يمكن أن تكلف أكثر من 100000 دولار إذا تم إغلاقها لمدة يوم واحد فقط، بأجهزة استشعار اهتزاز XY على كل محمل شعاعي، ومستشعر دفع، ومشغل طور واحد على الأقل. إذا كانت الآلة أقل أهمية وكان التأثير أقل من 10000 دولار في اليوم، فربما يكون مستشعر الاهتزاز الموجود على محمل جانب الحمل الأقرب إلى أداة التوصيل كافيًا. بين هذين الأمرين، من الضروري الحكم على أفضل طريقة لمراقبة الماكينة حتى يتمكن المصنع من الحصول على عائد على الاستثمار (ROI)، والذي قد يكون عبارة عن مستشعر واحد أو اثنين مع وظيفة التشغيل/الإيقاف (التنبيه/الإيقاف).
1. الآلات الدوارة
تعد المعدات والآلات الدوارة مثل المحركات والمراوح والتوربينات وناقلات الحركة من أكثر الأماكن شيوعًا لأنظمة مراقبة الاهتزازات. نظرًا لأن عدة أجزاء مختلفة تدور في وقت واحد وتنتج أنماط اهتزاز، فإن مراقبة الاهتزاز ضرورية للتأكد من أن جميع المكونات تعمل بشكل صحيح. بالنسبة للمعدات الدوارة، يمكن أن تؤدي المشكلة إلى تلف المعدات والفشل الكارثي. يمكن أن تساعد مراقبة الاهتزاز في تحديد الاختلال وعدم التوازن والاحتكاك وفشل المحمل وحتى مشاكل الرنين في الآلات الدوارة.
2. المحامل والتروس
في محامل وتروس الآلة، تحدث اهتزازات مختلفة بترددات مختلفة، وهذا هو سبب شيوع أنظمة مراقبة الاهتزازات. باستخدام التروس، يتم إنشاء عدد من أوضاع الاهتزاز المختلفة عندما يقوم الجهاز بمهمته المطلوبة. من الصعب للغاية مراقبة هذه الاهتزازات المتفاوتة من قبل البشر وحدهم، ويعتبر استخدام نظام المراقبة للإنذار المبكر أمرًا ضروريًا لاستمرار عمل الآلة.
3. الضواغط والمحركات والمضخات الترددية
تحتوي المعدات مثل الضواغط الترددية والمحركات ومضخات الإزاحة الإيجابية على مكونات متعددة بداخلها تهتز بشكل نشط. تتميز الآلات الترددية بأن أجزائها تتحرك بطريقتين: الدوران والخط المستقيم. تساعد مراقبة اهتزازات هذه المكونات المختلفة في تحديد الأعطال المحتملة قبل أن تتسبب في تلف الجهاز.
4. الجسور
تعد مراقبة الاهتزازات أمرًا بالغ الأهمية لضمان السلامة الهيكلية للجسور. يمكن أن تساعد اتجاهات الاهتزاز في إنشاء خط أساس لسلوك الجسر السليم وغير التالف، ومن ثم اكتشاف متى قد يواجه مشاكل هيكلية. إذا بدأ الجسر في إظهار سلوك اهتزاز غير طبيعي، فيمكن لموظفي الصيانة إجراء عمليات الفحص اللازمة لتحديد مصدر المشكلة.

5. السباكة
تعد أنظمة مراقبة الاهتزاز ضرورية لخطوط الأنابيب التي قد تكون عرضة للمشاكل الناجمة عن الاهتزاز. لا تساعد أنظمة المراقبة في التنبيه عند بدء ظهور المشكلات فحسب، بل تساعد أيضًا في العثور على السبب الجذري لمناطق المشكلات. وبهذه الطريقة، يمكن مراقبة المناطق عالية الخطورة على خط الأنابيب بحثًا عن المشاكل المحتملة.
تركيب نظام مراقبة الاهتزاز
يعد اتخاذ الخطوات اللازمة للتأكد من أن الآلات والمعدات تعمل بشكل صحيح ويمكن استخدامها لأطول فترة ممكنة أمرًا ضروريًا لأي عمل تجاري. باستخدام نظام مراقبة الاهتزاز لقياس أي حالات شاذة وتنبيهك بالمشكلات المحتملة، ستتمكن من مساعدة جهازك على العمل بكفاءة أكبر لفترة أطول دون التسبب في أضرار جسيمة.